The Old Mart and New Vision
The young people of a town get a poor press: disapproved of if they are visible or trapped online, in their rooms. In the Lanarkshire town of Biggar they benefit from a warm, non-judgemental place to gather.
Biggar Youth Project is a voluntary organisation which runs activities for High School age young people in Biggar, South Lanarkshire. They support them by providing a base for a range of activities, a place to gather and access hot food, food-share, computers, games and the emotional and practical support of the volunteers and staff that run the space.
As a valued and rooted local initiative funding came from local wind farms, with an obvious interest in low carbon solutions.
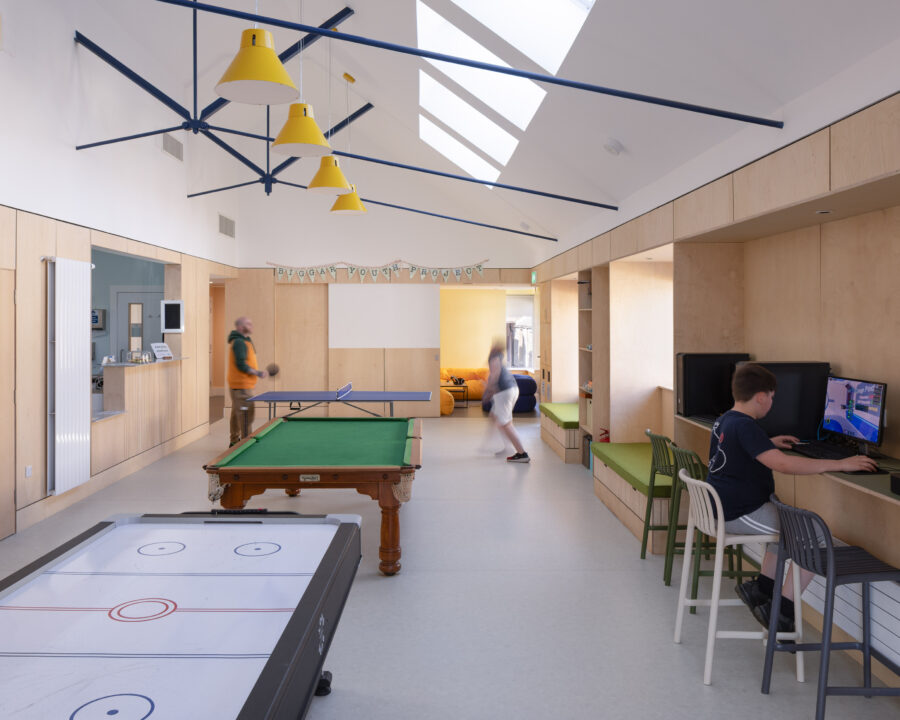
CLIENT / Biggar Youth Project
ARCHITECT / Fraser/Livingstone Architects
GROSS INTERNAL AREA / 162 m2
BRIEF AND CONSTRUCTION / Gathering Place for Biggar's Young People realised as a healthy low carbon retrofit
COMPLETION / January 2025
The space and building was originally part of the Town's historic livestock auction mart, dating back to the late 1800's and refurbished to become the youth centre in 2002.
The location sits nicely in the town, just off the High Street – the Town’s broad, linear, mediaeval Mercat – on the way in from the High School, so poised to scoop the young people up. But the 2002 refurb was extremely rudimentary, with the wind whistling through a dark and hard-to-find space, insulation minimal and heating costs astronomical, and alarming structural degradation in the main trusses.
The Vision for this newfurb evolved through design Seshies with staff, volunteers and, crucially, the young people, and was summarised as: warmth, trust, shared food; and, in more detail, converted the interior from a corridor with rooms off, to a big welcoming space with secondary and servant spaces and places off, including a cockpit kitchen counter at the fulcrum. Natural light was greatly improved by recovering the Mart’s original lines of roof glazing; and a wee window was opened at the High Street corner, to provide a glimpse of the town’s centre from the building, and a warm glimpse in, from the High Street, through the pend and up the close – of particular attraction on a dreich winter’s afternoon.
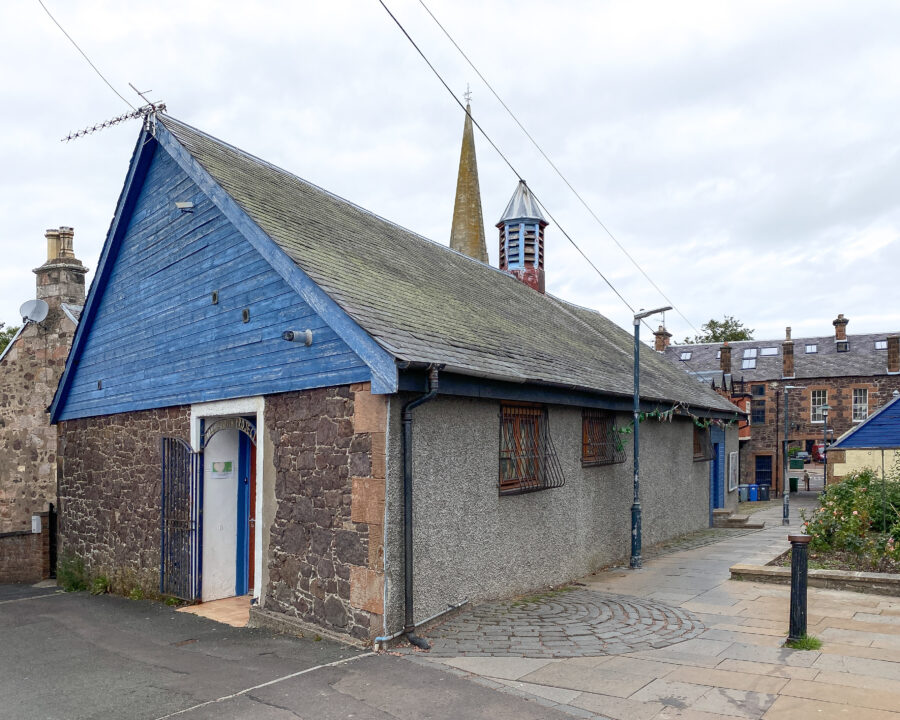
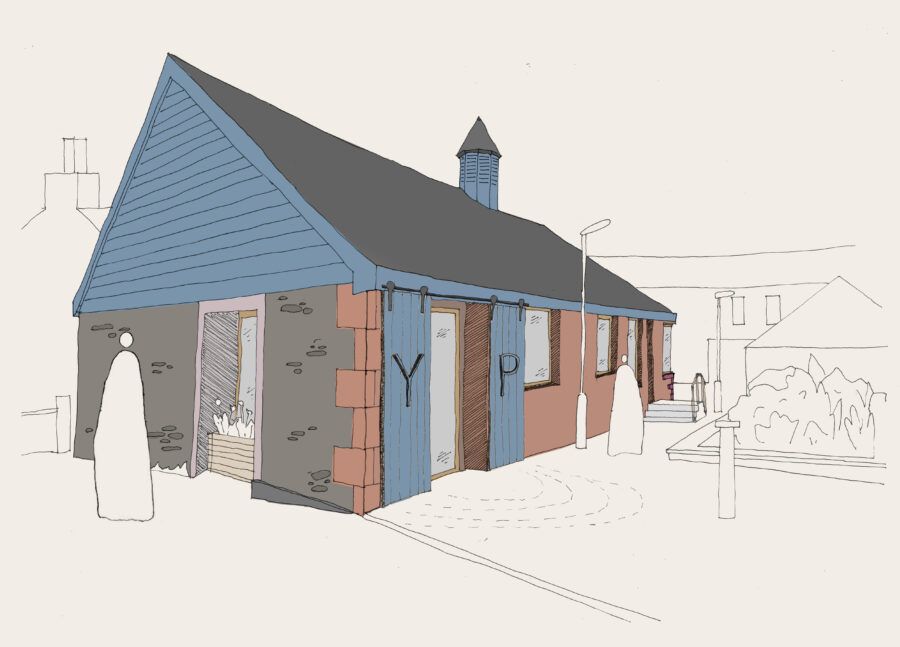
A Retrofit Exemplar
It’s now widely accepted – despite the persistence of demolition – that the greenest buildings by far are those sturdy ones from the past, with carbon and culture embodied, suitably upgraded. The urgent task facing us is therefore the upgrading of their fabric and heat generation; but this is usually done without the necessary understanding of how they move and breathe, and how to achieve the upgrades sympathetically.
Specifically, there’s been a historic change in building technologies, where pre-circa-1914 buildings are usually constructed from natural materials which move and breathe – tend to be vapour open, where the tiny molecules of water vapour permeate through fabric, while heat is retained if draughts are excluded. They also tend to accept some movement without cracking – lime mortar and structural timber being exemplars. Modern construction, in contrast, looks to seal a building with polythene vapour barriers, creating what is, effectively, a poly-bag, and stop all movement, both of the fabric and of moisture through it. The resultant tendency to trap moisture, which rots timber, is then treated with arsenic-based rot treatments or other toxins, and poisons and toxins are also introduced such as cyanide in the cheap, plastic PIR/PUR insulation that killed the Grenfell residents. Such highly-processed materials are not only toxic in any construction but, applied in retrofit, work against the nature of the historic building techniques so, for instance, where unventilated voids are created, damp is trapped and rot thrives.
Our mantra is, therefore: move and breathe, while insulating, avoiding unventilated voids, and cutting out draughts; then apply modern mvhr – mechanical extract ventilation with heat recovery – to achieve decent air quality without losing heat.
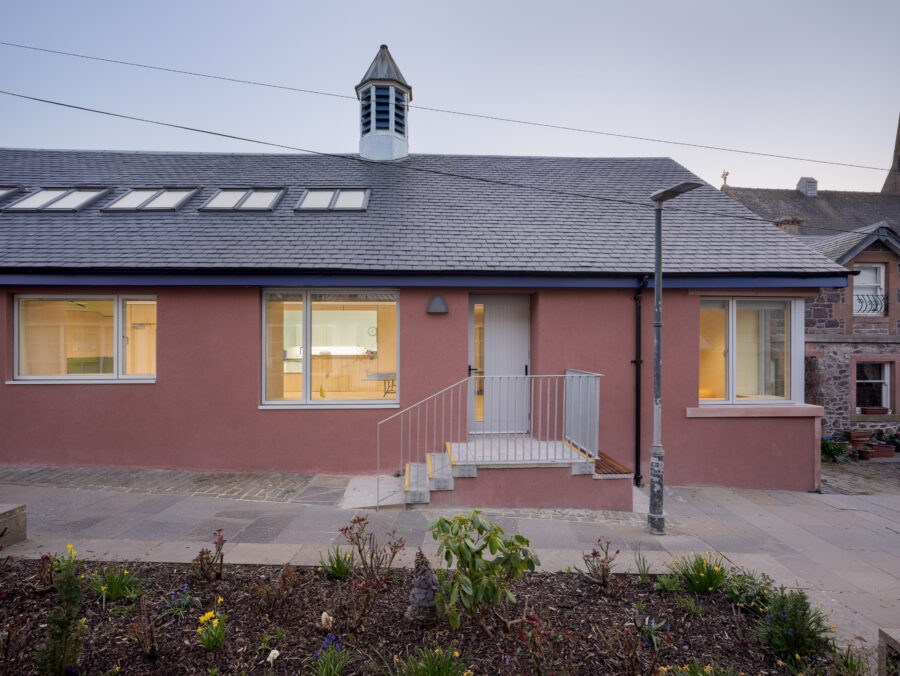
Specify For Health
We might start with what you might call the anti-Grenfell spec: do not specify poisonous, toxic, incendiary materials; do use natural, breathable ones – these are our young people, after all, and they deserve a non-toxic environment… though the same should go for all of us.
So: walls stripped of impenetrable layers – including gloss paints – and dubbed-out with Baumit breathable lime plaster to avoid voids; insulation to be hemp where possible (in roof – Indinature hemp, with huge carbon-sinking qualities and produced by a Scottish Borders start-up), wood-fibre where not (walls). The fabric remains breathable including continuous eaves-to-ridge ventilation, above the insulation and under the sarking. Walls reasonably airtight.
The energy source is then an air source heat pump, with mvhr – mechanical ventilation with heat recovery to remove water vapour but recapture and reuse heat from the exhaust air.
We architects also need to be upfront with Building Control and the application of their Standards: if they apply newbuild u-values to retrofit, then interstitial condensation is inevitable so, given the huge carbon gains from retaining old and sturdy buildings, relaxation is both reasonable and essential, to avoid condensation and rot. In proving this the standard tool is wufi calculations, and it is our contention that this examination should be required for all retrofit – its absence storing-up retrofit failure for the future.
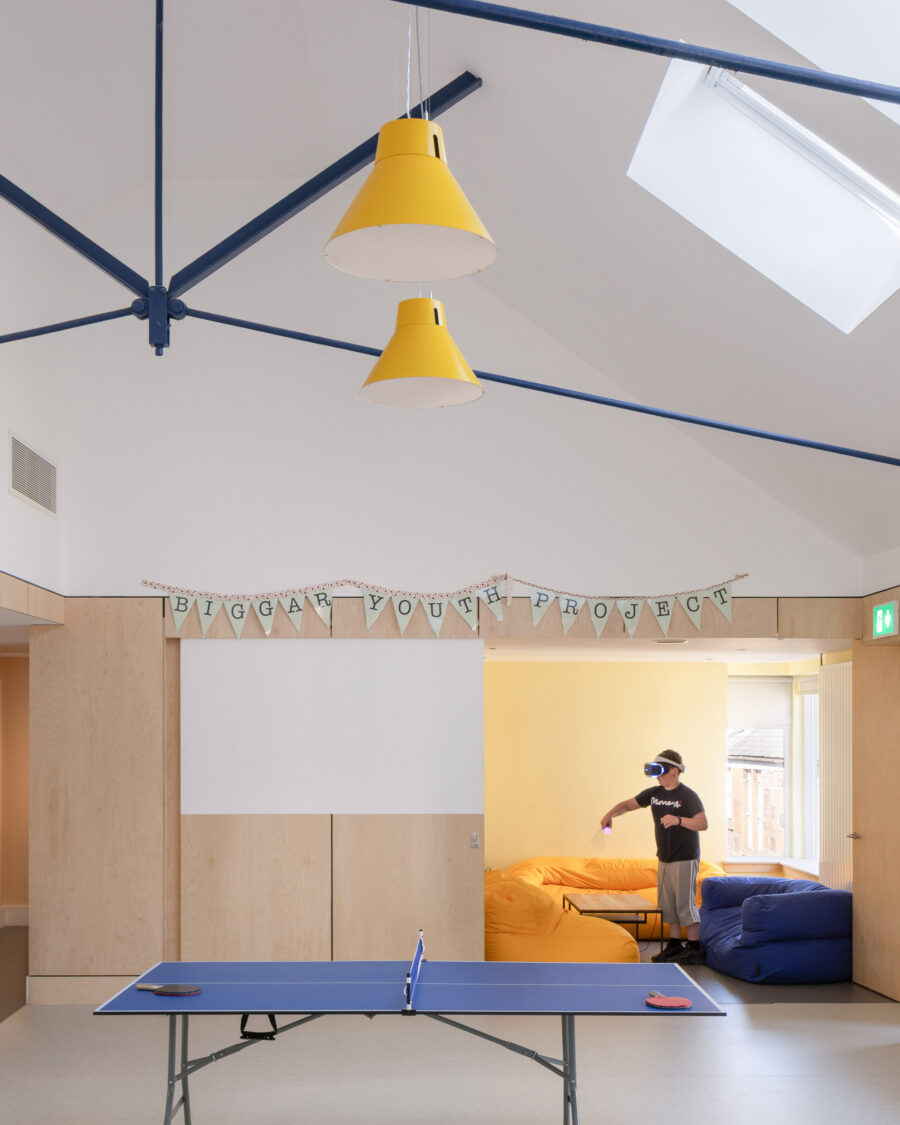
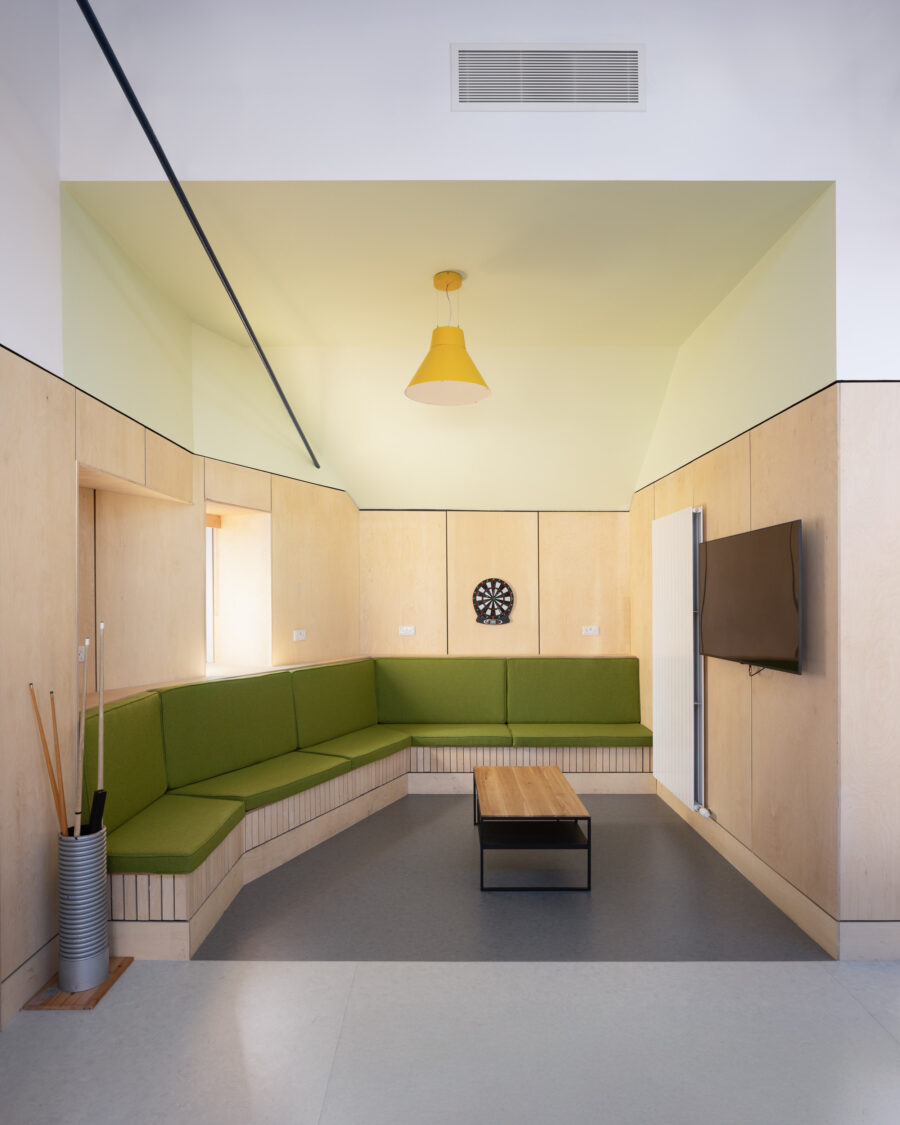
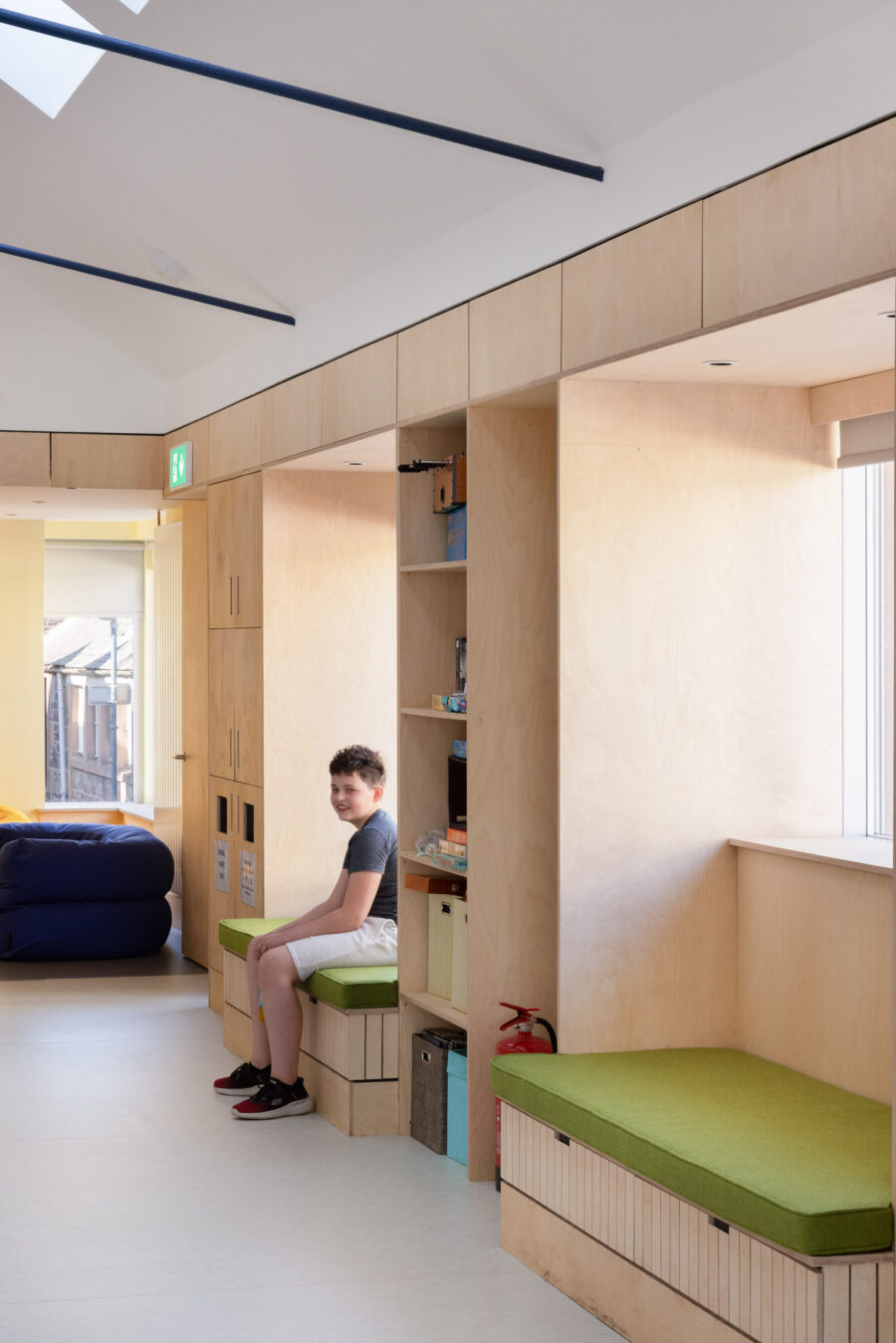
FLA TEAM / Fredrik Frendin, Malcolm Fraser, Emma Henderson
STRUCTURAL ENGINEERS / Elliot&Co
ENERGY, SERVICES / Carbon Futures/DKI Consulting Engineers
QUANTITY SURVEYORS / Hardies Property & Construction Services (Formerly David Adamson Group)
CONTRACTORS / McCann Builders, Biggar